Harald Fehringer has been Production Manager at MGG Metrec since November 2024. In this role, he is not only responsible for his team, but is also in charge of a wide range of technical equipment, including two shredder systems. Anyone who thinks this makes him nervous is wrong! He quickly masters his new position with calm and prudence.
Mr. Fehringer, you have only recently taken over responsibility for production management at Metrec. How did this come about?
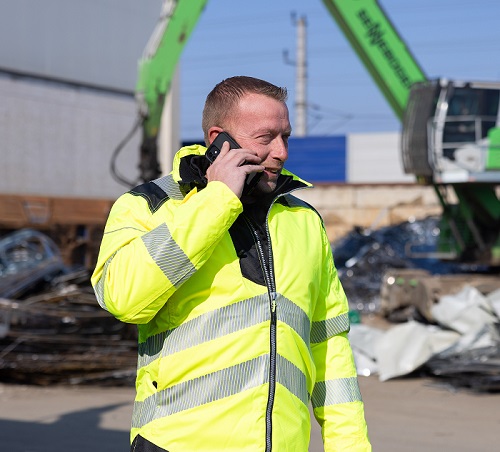
The most important tool for Harald Fehringer is his mobile phone. Being reachable is an absolute must for him and essential for his job as production manager.
Harald Fehringer: Yes, that’s right, I’ve been working for the Müller-Guttenbrunn Group for a long time, but I’ve only been in production management for a few months. In 2024, the company management decided to create a second position in Production Management, as the workload had been steadily increasing over the previous years. I applied for the position and was able to beat the other applicants at the hearing. I took up my new position in November last year. Unfortunately, my colleague recently left the company, which is why I am currently also responsible for his agendas.
That doesn’t sound like a zero-eight-fifteen situation. Especially considering that you were not yet fully trained.
Harald Fehringer: The situation really isn’t easy. However, I benefit from the fact that I’ve been working here at Metrec since 2001 and – if you exclude operating the two shredder systems – I’ve been through all the stations here on the site. I drove the loader for almost 15 years and can still operate every machine today if circumstances require it. And yet there were and still are many things that I had to learn and acquire, especially at the administrative level.
How did you approach this challenging task? Your teacher was no longer available.
Harald Fehringer: With calm and prudence. There’s no point in rushing around, it only makes things worse. Here at Metrec, we are in the fortunate position of having a great team structure. Colleagues like Michael Grimm and Manuel Riedl, to name but a few, have become something like mentors to me. They – and many other colleagues – are there to help and advise me. This enables me to acquire the necessary expertise quickly and unbureaucratically.
You have piqued our curiosity: What does a typical working day look like for you?
Harald Fehringer: I start by organising the employees and defining the daily schedule. I’m responsible for a team of around 30 people: loader drivers, excavator drivers, sorters, machine operators and shredder drivers. I then liaise with Amstetten station. Most of the communication takes place by e-mail. The weighing results of the transported material from the previous day are passed on and the number of wagons we need at the plant the next day is announced.
Then I go out into the yard, do my rounds and check that everything is OK. My colleagues can reach me on my mobile phone at any time and contact me if anything out of the ordinary happens.
When everything is running smoothly on site, I discuss with the management: how much of which material is currently available, what is coming in, what can be sold. We are in constant dialogue, including about changes to the daily schedule. It is not uncommon for things that have just been finalised to have to be discarded and rescheduled. For example, a special, unplanned delivery of materials can sometimes make us all ‘sweat’. It is then up to me to act quickly and take the necessary steps to get the situation under control again.
While we’re on the subject of materials: what route does the scrap take here on the site?
Harald Fehringer: Scrap is delivered by lorry or rail wagon. The loads are weighed and the delivered goods are inspected and assessed. If the material does not correspond to the quality, this is reflected in the price. The excavators carry out a rough sorting of the load. Heavy iron parts are sorted out, crushed in the shears if necessary and loaded for resale. Mixed scrap goes straight to the shredder and is shredded. The iron it contains is sorted out by a magnet and sold directly. The remaining material is taken to Metran for further processing. Cars are processed manually in the first step. Sorters dismantle tyres by hand and drain all fluids. They can then also be shredded in the shredder. The residual fraction is sent for incineration.
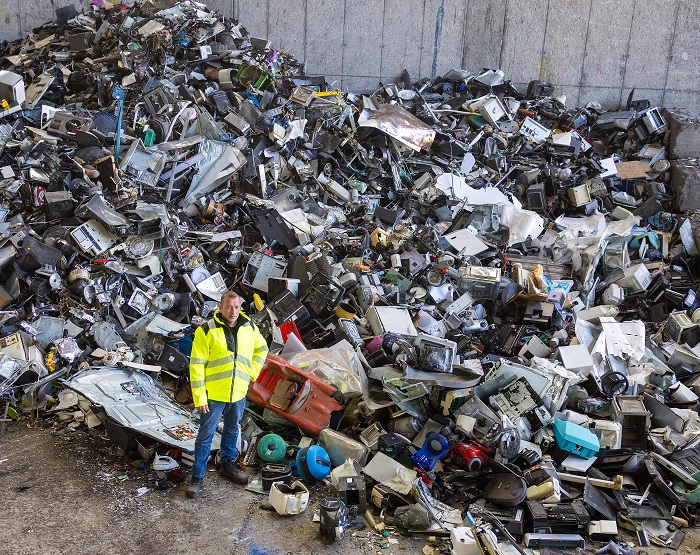
After coarse sorting, the e-waste is transported to the shredders. Small electrical appliances such as mixers, hoovers and children’s toys are processed in the ‘EVA shredder’ into two different coarse fractions.
What happens to electronic waste? Is it also processed in the large shredder?
Harald Fehringer: Only large electrical appliances such as washing machines go into the large shredder. The majority of electrical appliances to be scrapped are much smaller and can be processed in the EVA shredder. Small electrical appliances such as mixers, hoovers, children’s toys and much more should be delivered without batteries. Sorters go through the material anyway and remove any rechargeable batteries and batteries that are still present in the appliances and secure them in the boxes provided. If rechargeable batteries or batteries get into the shredder anyway, this can lead to deflagrations or even fires in the system. A sophisticated monitoring and alarm system as well as an extinguishing system prevent the occurrence of fires in such exceptional cases.
The shredded material comes out of the shredder in two different fractions – one coarse and one fine – and is transported to Metran in Kematen an der Ybbs for further processing. The residual fraction is sent for incineration.
Who takes care of the maintenance of the shredders and what happens if a shredder breaks down?
Harald Fehringer: Maintaining the systems is part of the morning routine. The shredders, which are shut down at the end of the working day, are started up and inspected. Fitters check the machines to make sure they are working properly, replace wearing parts if necessary and repair anything that has broken. This takes about an hour. If major repairs or maintenance work is required, a shredder may have to be taken out of service for several days or weeks. If this happens unscheduled, intervention is required.
How long can scrap be temporarily stored on the site without being further processed in the shredder plants?
Harald Fehringer: With the large shredder, we can temporarily store delivered material for a week without processing it. After that, deliveries have to be stopped. The e-waste for the smaller EVA shredder has to be stored in the hall, protected from the weather. Here, our capacity limit is reached after just two days. If a plant is unscheduled and does not run for a longer period of time, it is up to the management to decide how to proceed.
What qualifications do you need for your job and what do you particularly like about your work?
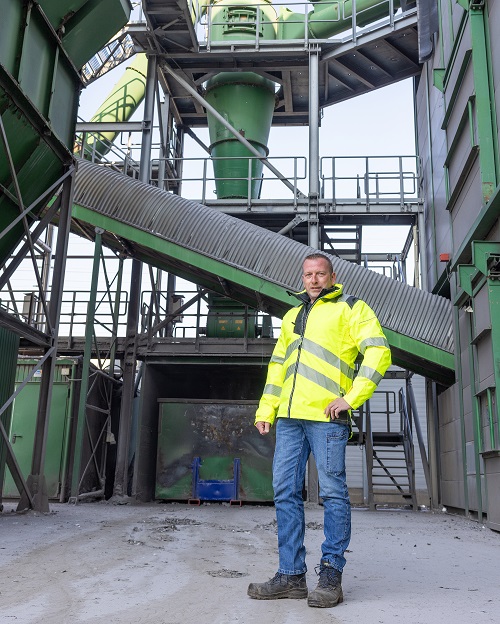
Harald Fehringer’s area of responsibility includes ensuring that the systems run smoothly. With his many years of experience and a great team at his side, he is ideally equipped for the challenges that his job entails.
Harald Fehringer: When I started at Müller-Guttenbrunn in 2001, you had to have learnt a metalworking trade. I am a car body fitter. You learn everything else you need to work here on the site from your colleagues. There is no apprenticeship. I learnt everything from scratch. In my current position, you also have to be able to deal well with your employees. Each person is individual and you have to be able to empathise with the people you are responsible for. This is another new challenge for me, which I don’t find difficult and which I am happy to take on. In general, I can say that I am in the fortunate position of being able to pursue an activity that fulfils me and that I enjoy. It’s the sum of the whole, the variety, that makes my work so special.
How do you see the Müller-Guttenbrunn Group in general as an employer?
Harald Fehringer: We have a perfect environment here. We cultivate a respectful ‘you’, the team spirit and helpfulness among colleagues is great. I enjoy going to work and look forward to seeing everyone again after two weeks‘ holiday. The fact that everything is going so well is certainly also due to the fact that the company is managed well and prudently by the Müller-Guttenbrunn family and the employees are not just ‘a number’.
Last but not least, we are interested in Harald Fehringer as a private individual. Would you like to tell us a little about yourself?
Harald Fehringer: I am 45 years old and live with my wife and our two children in Mauer near Amstetten. My daughter is almost grown up at the age of 20, while my son is only five and keeps us on our toes. I spend most of my free time with my family. I’m a member of the Hausmening fire brigade, but I don’t currently go on any missions. I also spend a lot of time looking after our house and garden. However, I have to say that I don’t have ‘green fingers’ and am therefore more responsible for repairs.
Harald Fehringer – a man in demand with a limited time window
We would have liked to talk to Harald Fehringer for longer, but his phone rang several times during the interview. He calmly typed a few messages in response or signalled to the caller with a brief ‘I’ll get back to you in a minute’ that he would take care of it. But now he is signalling to us that his presence is required on site. Without rushing, he takes us to the exit and bids us a friendly farewell. Thank you very much for the conversation!