Generating energy with a power plant on your own roof: photovoltaic systems are on everyone’s lips and have experienced a real boom in the recent past. But what to do when the photovoltaic panels are no longer needed? To provide answers to this question, intensive research is being carried out – by the Müller-Guttenbrunn Group and others – into a complete recycling and utilisation process for photovoltaic modules.
The question of what to do with photovoltaic panels is often only asked by owners and operators of photovoltaic systems when they are no longer functional or no longer profitable. What to do with the panels that cannot be disposed of in conventional waste collection centres? Who takes them back? Are there any costs involved?
In principle, manufacturers are obliged to ensure that the panels they produce are disposed of properly or, much more sustainably, recycled properly. Research is being carried out around the world to separate the individual components of PV-modules in such a way that they can be reprocessed or recycled. And time is pressing, because in view of the hype surrounding the ‘power plant on your own roof’ – fuelled by extremely high energy costs – many PV-systems will be replaced with more powerful models in the medium term, raising the question of what happens to the old modules.
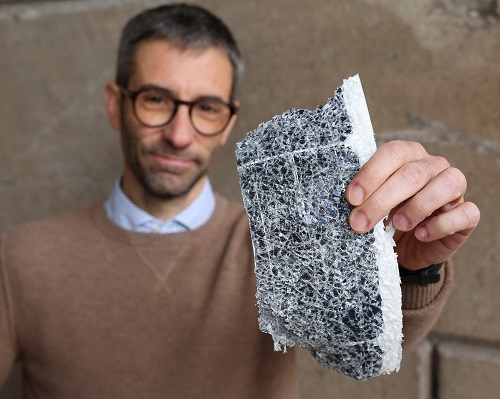
The biggest challenge in recycling PV panels is the glass plate, which is bonded to other components such as silicon. These bonds need to be loosened.
The status quo: There is still a lot to do.
The Müller-Guttenbrunn Group is intensively involved in national and international research projects. But that is not all. We have also been researching possibilities in this field internally for some time. The challenge here is that the largest material component, the glass plate, is bonded to a background film and other components – such as silicon. This bonding has to be solved. And to do so in such a way that the process of separation and subsequent recycling can be converted into an economically viable process.
At MGG Metran in Kematen an der Ybbs, the aluminium frame (approx. 10% of the total material) and the plastic parts on the back of the panel are currently separated from the laminated glass pane. The modules are first shredded and crushed. The non-ferrous metals are removed in the ‘Metran witch boiler’ and the metals are returned to the material cycle in melting operations.
Various recycling methods for the glass fractions are currently being examined and tested. However, this procedure can only be a temporary solution at best. ‘This approach is only a first, very small step in the right direction,’ explains Daniel Forstner, who is responsible for research into PV recycling at Metran. „The aim must be to turn old photovoltaic panels into new photovoltaic panels. But the industry is still miles away from this. Photovoltaic modules are mainly manufactured in China, so this is a long-term goal“.
Over the past few months, Daniel Forstner has held numerous discussions with companies that could possibly process the shredded laminated glass. Of course, it would be best if the used glass could be turned into new glass for PV modules. But even this solution will only work if a way can be found to separate the glass from the coatings in an economically viable way.
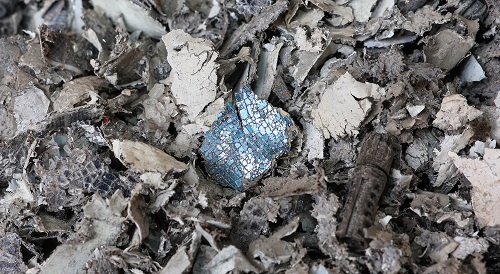
The aim must be to produce new photovoltaic panels from old ones. Or that systems can be put to further use.
Apollo and PVReValue – research projects with Metran participation.
In order to broaden the scope of the topic, Metran is participating in Apollo, a scientific Horizon project of the EU, which is working on producing PV panels from PV panels again. International expertise is being pooled here under the leadership of experts from the Fraunhofer Institute in Halle an der Saale. Also involved is a PV manufacturer from Turkey, which – as the only one in Europe – combines all the business units required for the construction of PV modules in its company. A valuable supplier with a wealth of practical experience and expertise.
Apollo’s vision is to create a circular economy by recycling all PV materials to a high quality. The aim is to increase material recovery from 18% to 93% through five innovative processes: sorting, extraction, refinement, reuse, tracing & circularity.
The Austrian Research Promotion Agency FFG has also funded a project with PVReValue, in which the University of Leoben acts as coordinator. The Müller-Guttenbrunn Group is also involved here as a project partner in order to actively promote the topic.
The innovative content of PVReValue lies on the one hand in the multi-stage compound separation, which causes a pre-fractionation of the fractions to be further processed. On the other hand, it lies in the complex combination of further processing methods for the fractions obtained. The high quality of the process begins with the input characterisation, whereby modules can be selectively batched and output qualities can be modelled and adjusted accordingly. The project thus generates high-quality recyclable secondary raw materials in the sense of a functioning circular economy.
2nd Cycle: Austrian start-up power for the topic of PV reuse.
The Müller-Guttenbrunn Group is expanding its activities in the field of photovoltaic recycling with an innovative approach by acquiring a stake in the Amstetten-based start-up 2nd Cycle. Instead of immediately recycling used PV modules, 2nd Cycle pursues a reuse-first approach: modules are automatically tested and – if technically possible – fed into a second life cycle.
In addition, 2nd Cycle also offers integrated recycling processes for non-reusable modules and, with the SolarBox, an intelligent logistics solution for safe and efficient transport. MGG is contributing its many years of expertise in recycling technology and material flow management to this partnership in order to actively shape the development of a sustainable, closed recycling chain for PV modules.
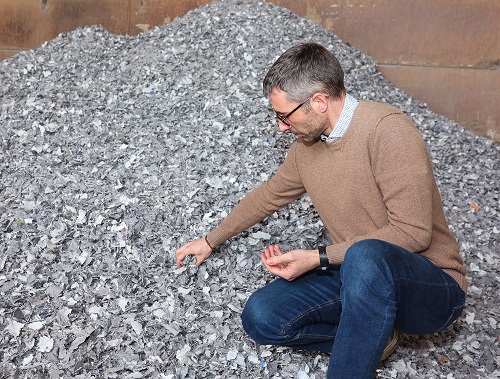
Daniel Forstner ventures a look into the future of photovoltaic recycling: „Economic considerations will show the direction in which the recycling or reuse of PV modules is heading“.
Cenelec-certification for MGG.
The Müller-Guttenbrunn Group has had its recycling processes for large and small electrical appliances certified in accordance with Cenelec. Since December last year, the company has also had a corresponding certificate (Cenelec EN 50625-2-4) for the acceptance and further processing of photovoltaic modules. For this, specified recycling quotas and processing guidelines must be observed. There are strict limits for cadmium, selenium and lead to ensure that the removal of harmful substances functions correctly. These limits ensure that only silicon-based modules have been processed. There are also so-called thin-film modules on the market, which correspond to a different technology and are categorised by law as hazardous waste.
Looking into the crystal ball.
Daniel Forstner ventures a look into the future of photovoltaic recycling: „Economic considerations will show which direction the recycling or reuse of photovoltaic-modules will take. The fact that cheap goods from China are pushing onto the market and thus making recycling efforts more difficult – as in other sectors – should not be ignored.“ At present, we can see that the photovoltaic boom has peaked for the time being. Demand is stagnating, probably also because a high degree of saturation has been reached. „What is certain, however, is that the recycling industry will be faced with a large quantity of used PV panels in a few years‘ time. I hope that by then we will have found a good solution to close the product cycle in the PV module sector as well.“