After more than ten years in daily use at MGG Metrec in Amstetten, the time had come: the powerful Thyssen Henschel scrap shears (built in 2004), one of the central systems at Metrec, underwent a general overhaul.
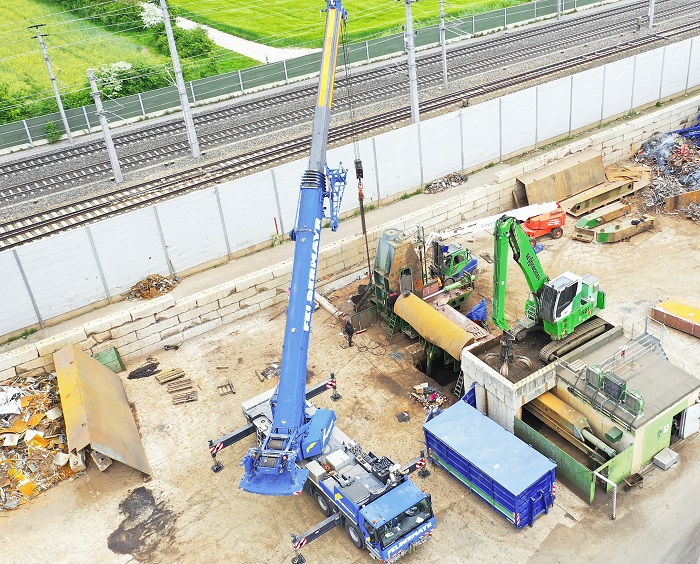
After around ten years, the shears at MGG Metrec underwent extensive maintenance.
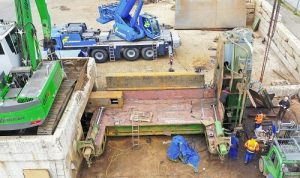
Maintenance of the wear plates was at the centre of the work on the Henschel shears.
In close cooperation with Metrec’s internal maintenance department and an experienced external partner from Germany, the system was completely dismantled, cleaned and re-plated in spring 2025. The focus was not on replacing entire components, but rather on the targeted repair of the wear plates that protect central components such as the tamper and blade carriage. The shears are lined with numerous wear plates, which only have a limited service life. Most of them are worn out after around ten years. The system was therefore completely dismantled. All the wear plates were checked, the base material was rewelded and the shears were repaired. The entire maintenance was successfully completed within just four weeks and the Henschel shears were able to go back into operation at the end of May.
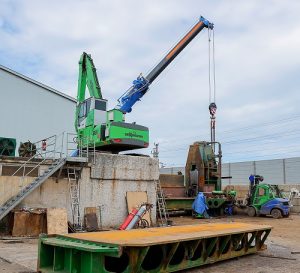
All of the shear’s wear plates were checked, the base material rewelded and the shear repaired.
„A project straight out of the textbook!“
For Metrec Managing Director Michael Grimm, it’s a project straight out of a textbook: „You have to know: There is no fixed maintenance schedule for a shear like this – maintenance is carried out flexibly, depending on the actual wear and tear. The entire maintenance project worked perfectly. I would like to thank all my colleagues who were involved in the realisation – from planning and dismantling to the final recommissioning. The overhauled shears are now back in operation eight hours a day and are making a significant contribution to the smooth processing of our scrap types.“
The fact that everything went according to plan is also due to the experience of the Metrec team. This is because similar maintenance work was carried out on the same system ten years ago. Thanks to the experience gained back then, the current project was implemented quickly and smoothly.
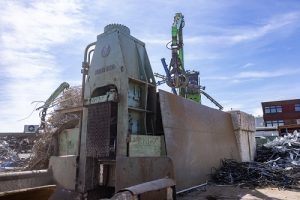
The shears at Metrec process a wide variety of scrap types made of construction steel from a material thickness of three to four millimetres, which are efficiently shredded by this system.
The Henschel Shear – a centrepiece at Metrec.
Modern scrap processing is hardly conceivable without powerful machines. One of the key technologies in this area is the so-called Henschel shears. These are large hydraulic shears that have been specially developed for cutting scrap metal. It is named after the long-established Henschel company, which was a leader in the development of such machines for a long time.
The Henschel shear is a stationary hydraulic scrap shear with a high cutting force. It is used for shredding large, solid metal parts – including railway tracks, beams, pipes, sheet steel and more. The metal is not milled or sawn, but mechanically separated by pure shear forces. This enables large quantities of scrap metal to be processed quickly, efficiently and economically.
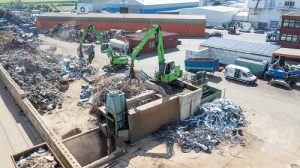
Due to the maintenance break, a lot of material has accumulated for processing with the Henschel shears.
Three 90 kW electric motors enable an electro-hydraulic cutting pressure of 1,000 tonnes, allowing the shears at Metrec to process a wide variety of scrap types made of construction steel on a daily basis. Material thicknesses from three to four millimetres are efficiently shredded by this system – everything else is handled by the other systems at Metrec’s.
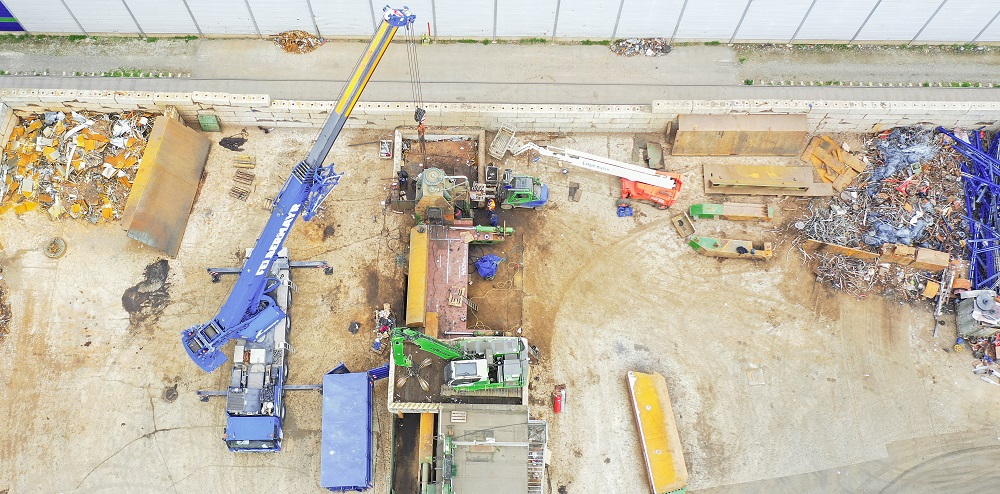
Thanks to the experience of the Metrec team, the dismantling and recommissioning of the scissors went without a hitch.
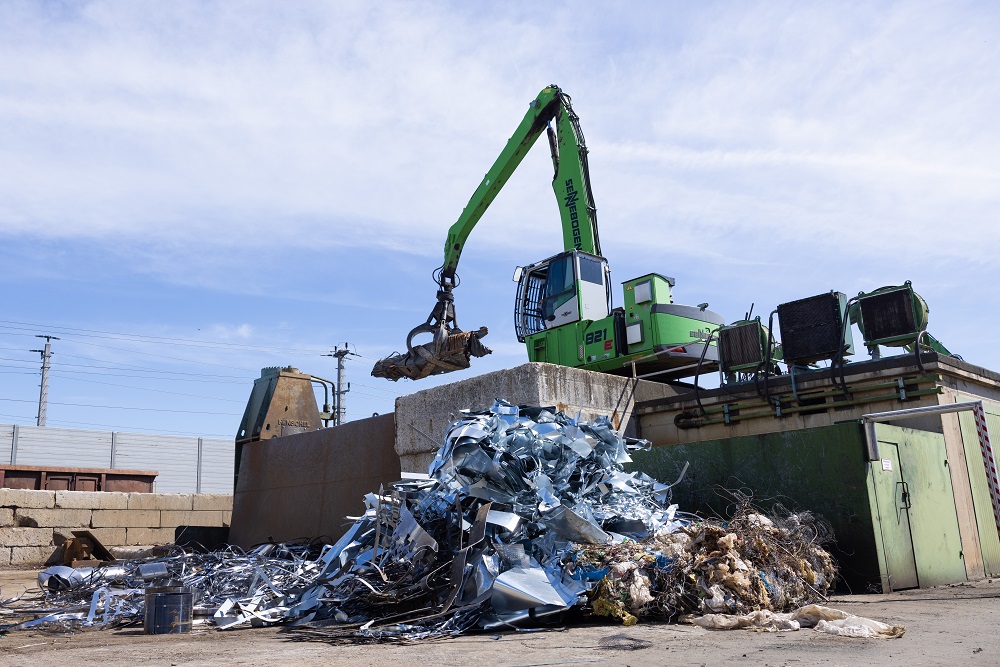
After four weeks of maintenance work, the Henschel shears at MGG Metrec are back in operation.
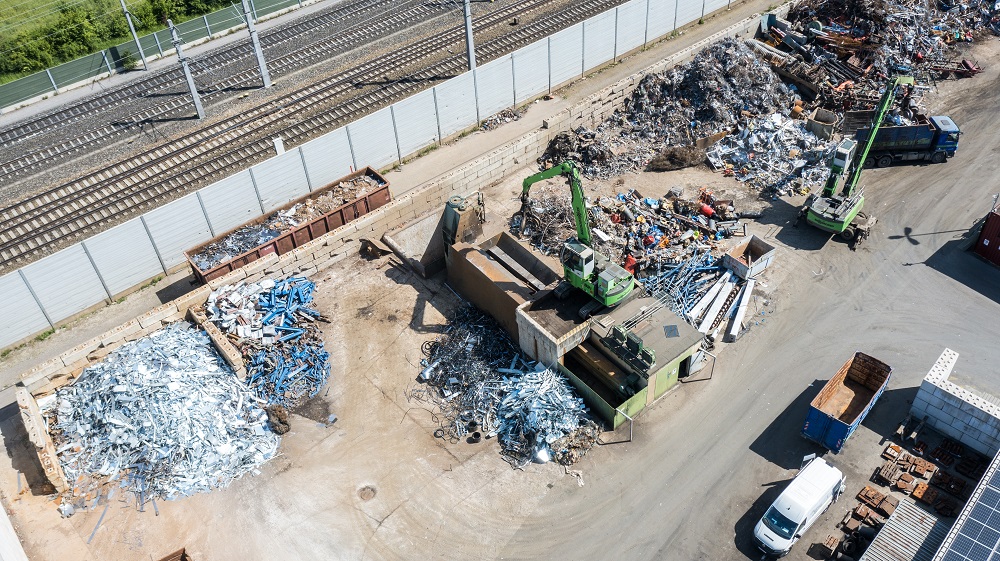
Since the end of May, the three 90 kW electric motors have once again ensured that a wide range of different types of steps can be shredded.