Patrick Hofer often sees his job as a game of chess. As shift supervisor, he assigns people to the appropriate machines, creates shift schedules according to material availability and ensures that the right material is available at the right machines. His constant companions are his radio, mobile phone and a large portion of calm and composure.
Mr Hofer, you have been working for the Müller-Guttenbrunn Group for 13 years. What made you decide to apply for a job at MGG Metran?
I was in a job that didn’t fulfil me and that involved a lot of overtime and little time for my family. My circle of friends and acquaintances knew about this and one day an acquaintance advised me to apply to Müller-Guttenbrunn because they were looking for people.
What happened next? You obviously got the job?
Yes, I was accepted, which I was really happy about. The job at MGG Metran had many advantages for me. The route to work was shorter, I had more free time due to the shift work and the elimination of a lot of overtime and – as a bonus – the job also paid better. This was extremely important in my situation at the time, as I had bought a house that needed to be renovated and made ready for my family.
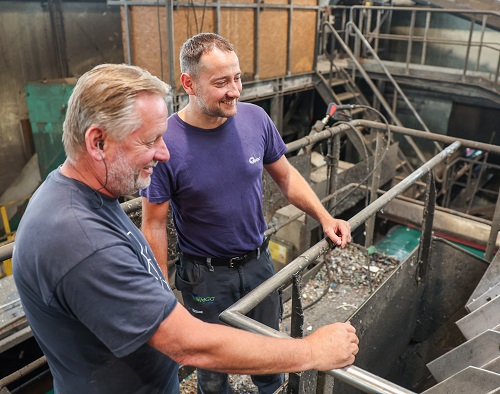
Patrick Hofer with his colleague Gottfried Zettl on the HMS (Heavy Medium Separation). For the shift and production manager, it is important to keep a constant eye on the processes at the plants.
What position was that back then?
At the beginning, I was kind of „passed through the company“. From one plant to the next to familiarise myself with the plant and the materials we deal with here. After a few weeks, I ended up in HMS (Heavy Medium Separation).
Do you have to have previous professional experience?
No, not at all. What you do need is a certain understanding of machines and technical processes. I learnt everything else from my colleagues. You can start up the system and switch it off again relatively quickly. It takes years to deal with all the pitfalls and the special troubleshooting options for various error messages. You’re constantly learning from your colleagues who have been with you for longer. At the same time as working on the HMS, I was also employed as a loader driver.
How long have you been a shift manager at Metran and what challenges does this position entail?
After 10 years at HMS, I was offered the vacant position of shift or production manager. I had the confidence to take on this position and a few days later I was told that I had got the job.
My job is to ensure that the shift operation runs smoothly. In concrete terms, this means making sure that all the systems are running, the material flows are functioning and – very importantly – that my colleagues are perfectly organised within the shift. What sounds relatively simple in theory is often a difficult task in practice. You have to maintain an overview in every situation, react quickly to changes and communicate well with your colleagues so that everyone is immediately informed of the new circumstances. Conversely, I have to be able to rely on my people to give me the necessary feedback, which I can then use as a basis for my future decisions.
This begs the question: What about predictability? There seem to be a lot of variable factors within a shift.
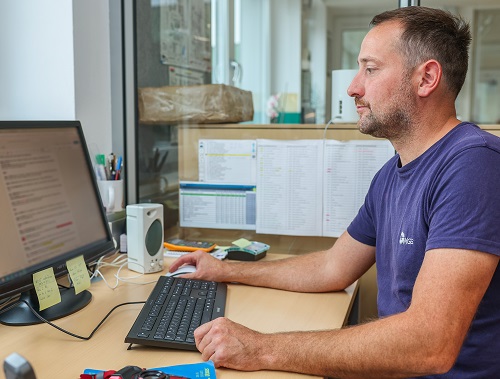
When Patrick Hofer is not out with his people at the plants, he coordinates the processes from his desk.
I am responsible for up to 19 colleagues on a shift who have to be scheduled. Not every person can operate every system. This fact becomes interesting when someone is absent, i.e. on holiday or sick leave. The shorter the notice of absence, the more challenging it can be to find a replacement. This often necessitates major shifts, especially during the main holiday period, which can sometimes even be shared between shifts.
But it’s not just the people who need to be organised, the material flows also need to be coordinated. Is there enough material available at each plant, when does it need to be „topped up“ or is there even enough raw material in the plant? Some plants process material that is delivered directly, while others continue to process what has already been pre-treated within the plant. Here, too, it is important to channel the flows in such a way that all systems can be operated and no system „runs out“ of material. In fact, shift schedules often depend on which or how much material is delivered. Long-term scheduling of shifts is only possible in the rarest of cases, with short-termism prevailing for the most part. And then it can also happen that technical problems occur, which then have to be resolved internally as quickly as possible.
Let me come back to the human component. Isn’t that the most challenging part of the whole thing?
That’s certainly true. As a shift manager, I have to deal with a wide variety of characters, so sensitivity is required. The team structure is extremely important, the team has to be kept together. It only works here if everyone gets on well together. The times when we used the well-known „crowbar“ are – thank God – long gone. If things do get heated, it’s important to keep calm and find a compromise. It’s also up to me to motivate people and create a good atmosphere. Sharing a coffee, a pizza or even a beer at the end of a shift helps to promote team spirit.
Is there such a thing as a „typical working day“ for you?
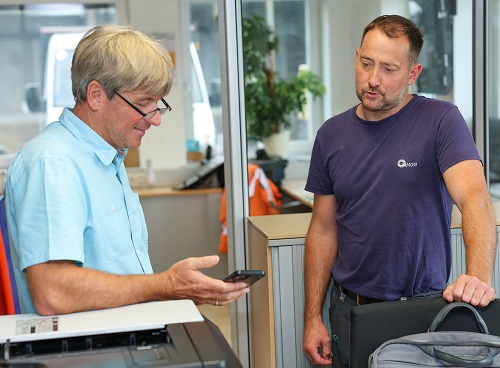
Patrick Hofer is not only the point of contact for his colleagues on shift. Interdepartmental communication and communication with the management – here in conversation with Martin Kriegl – are also on his agenda.
Typical is that every day is different. Nevertheless, there are a few fixed points. I always phone my shift manager colleague in the evening to bring us up to date. Have there been any problems? Are repairs necessary or still in progress? Will everything be finished as planned? We can’t afford to go into our own working day „blind“ in the interests of efficient collaboration. I then start my shift by unlocking all the halls, starting up the compressors and inspecting the material. My colleagues arrive shortly before five, we talk through the most important things and then we start on time.
From this point on, the radio and telephone are my constant companions. I start organising and adapting the day’s schedule. I answer my people’s questions over the radio: What material is going where? Which box is free? What comes next? I constantly correct the procedures on the computer and adapt them to the situation. The loader drivers have a tablet in their vehicles that informs them immediately of any changes. I also make the announcements over the radio on an ongoing basis. But I also rely on my colleagues outside to give feedback and provide information. We organise the day together.
I’m sure you’re well occupied with that. But I can imagine that you still have one or two special tasks to fulfil?
I’m not only shift manager, but also production manager. As such, I am responsible, among other things, for analysing the mixing material delivered. Gunther Panowitz makes the supplier a financial offer based on our analyses. If the offer fits, the material is delivered to us, if it doesn’t, another recycler gets the contract.
When new people are hired, we also need to be able to judge after a while whether the new colleague is up to the job requirements or would perhaps be better off elsewhere in the plant. Together with my colleagues, I am also responsible for ensuring that the maintenance intervals for the systems are adhered to.
In the 13 years that you have been with the Müller-Guttenbrunn Group, has there been a special experience that you would like to tell us about?
THE moment for me was when I learnt that I had been accepted for the position of shift and production manager. The fact that the company management placed their trust in me out of all the applicants will always remain a great moment in my memory.
What do you find special about the Müller-Guttenbrunn Group?
Although the company is a respectable size and also operates sites abroad, it is run in a very family-like way. As an employee, you are not just a number, as is often the case in other companies. Our boss, Christian Müller-Guttenbrunn, visits the factory several times a week. He is always friendly and happy to make small talk. He takes an interest in his employees, which is motivating.
The company’s internal events and excursions, which are not a matter of course, are particularly popular. Just recently, this year’s Kart Trophy took place. It’s always a highlight and we have a lot of fun together.
Another great thing about MGG is that you can climb the career ladder, regardless of your profession. I am the best example of this. When a position becomes available, everyone has the chance to apply for it and get it. That spurs you on to give your best.
When you look to the future: Where do you think the challenges will lie?
The most important thing will be to increase efficiency. The material supplied no longer has the quality it used to have. It has often already been through other recyclers and only contains what they were unable to extract. It is now up to us to develop processes to work with this „deprived“ material and earn money with it. A major challenge, but one that is absolutely necessary. This is the only way we can relieve the burden on our environment and promote the circular economy.
Speaking of the circular economy: has your approach to sustainability and recycling changed since you joined the Müller-Guttenbrunn Group?
Separating waste has always been a matter of course at home. My parents emphasised this. We didn’t buy anything nonsensical, old things were recycled or disposed of appropriately. Of course, my approach to this topic has been reinforced by my work at MGG-Metran. And I also brought up my children with this in mind.
Saving the best for last: what is Patrick Hofer like in his private life?
I am married and have two daughters (aged 19 and 21) with my wife. We live together in our house in Neufurth, which we bought a few years ago and have been renovating step by step ever since. I enjoy working in the garden, where I also like to relax by the pool in summer.
One of my great passions is cars, I own an Audi S6 Turbo, built in 1996. As I am a trained car mechanic, I like to tinker with it and repair more than I drive (laughs).
Another of my hobbies is actually Lego bricks. I’ve been involved with Lego’s Creator line for many years. Since we’ve been living in our house, I have even more space for them.
Mr. Hofer, thank you very much for the interview and all the best for the future!