As part of a multi-year investment programme – known internally as „Growth Strategy 2030“ – plastics recycler MGG Polymers is currently expanding its plant in Kematen an der Ybbs. More than six million euros are currently being invested in a new logistics centre. This will equip the plant for future tasks and make it fit for future challenges. In addition to a warehouse with an adjoining office building, a racking warehouse, four loading silos and sufficient space for internal transport have been created on an area of 7,000 m².
MGG Polymers‘ 2030 growth strategy is based on the assumption that interest in sustainable plastics and sustainable plastic products will increase in Europe in the medium and long term. This is also evident from developments in the relevant European regulations. In the plastics recycling industry, it is assumed that the growth of sustainable plastic products in Europe will increase in the future. Those responsible at MGG Polymers expect sales of recycled plastic supplied to European countries to at least double in the next five to ten years.
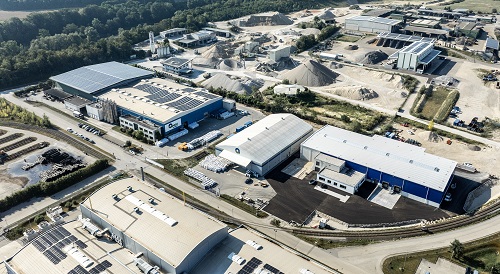
The structural extension will enable the logistics and material flows within the company premises to be optimised.
However, the growth strategy should also form the basis for leading the company into a successful future. MGG Polymers celebrates its 20th anniversary in 2025. Innovations and investments need to be made in order to optimise existing systems and to accelerate the development of new processes.
In the future, Polymers wants to develop new products and new product segments in addition to the product types that have been successful to date in order to remain a pioneer in the industry.
MGG Polymers currently produces – by adding various additives to the respective base plastic – around 60 product types, which have recently been accommodated in the newly built warehouse. As production „on demand“ does not fit into the company’s operational model, the challenge is to satisfy customer demand with the most continuous production possible and minimal changeover. Polymers must guarantee its customers security of supply so that their production processes can run smoothly. This requires an appropriate stock level. The conditions for this have now been created with the construction of the new warehouse, which is reserved exclusively for the storage of finished products.
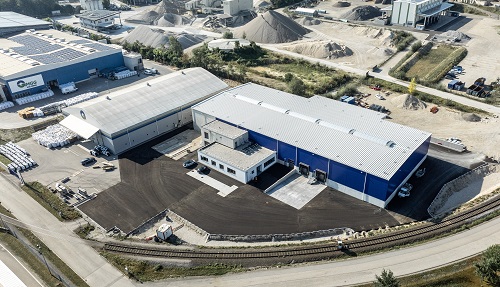
A two-storey office building was constructed adjacent to the new product warehouse, providing space for the entire logistics team.
Logistics centre for improving internal processes
In addition to the new logistics centre, the volume flows within the company premises in Kematen an der Ybbs are being reorganised to improve internal processes. New entrance and exit gates have been created in the north and south-eastern areas, and the weighbridge and radioactivity measurement system have been relocated accordingly. In future, raw materials will be delivered to the east of the company premises. The newly built warehouse is used exclusively for finished goods, which are stored in bags on pallets or in big bags. The racking system extends over three floors and therefore makes optimum use of the height of the hall. A remote-controlled shuttle system moves the goods to the desired position in a time-saving manner, replacing the time-consuming and often difficult positioning using forklift trucks.
A two-storey office building was erected next to the new product warehouse, which houses rooms for the logistics team, sanitary facilities and ancillary rooms as well as a technical room on the upper floor. The entire building complex is heated – sustainably and completely free of fossil fuels – by underfloor heating powered by heat pumps. The installation of a PV system is being planned and is expected to be realised in 2025. The product warehouse will be completed by four loading silos so that the products produced can also be delivered to customers in silo lorries.
Günther Höggerl, Technical Managing Director of MGG Polymers, is more than satisfied with the new internal logistics and the associated changes:
‘As our location in the Kematen an der Ybbs business park is limited in terms of space, but our concept includes the fact that our product will continue to be manufactured at this location, there was a need for action. After 20 years, we urgently needed to optimise the logistics and material flows in the limited traffic areas at the plant.‘
Sufficient time for planning enabled perfect implementation
The planning phase for these expansion steps took around two years. The collaboration between internal employees and external decision-makers was intensive and characterised by great commitment. As Polymers was aware that the legal framework would pose a major challenge, the decision was made to involve the relevant authorities on an ongoing basis during the planning phase. Project manager Christian Neumann attended many meetings in this regard and is certain: ‘In retrospect, I can say that it was one of the best decisions to proceed in this way. The dialogue atmosphere was relaxed and many things were clarified in advance by mutual agreement.’
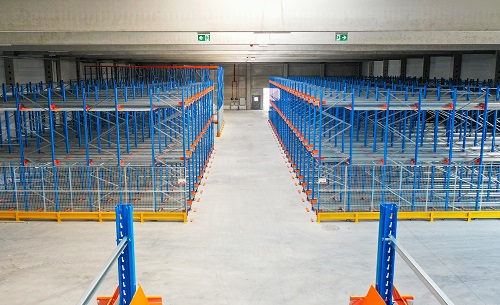
Sufficient storage capacity for the future.
The practical realisation of the project finally began in October 2023. Both Günther Höggerl and Christian Neumann are full of praise for the regional partner companies: ‘The support we received from our partners PSB – Markus Schnabl, the construction companies Pöchhacker Bau and Lehner Bau, Dachzentrum Haberhauer and the installation company Steiner – to name just a few – was excellent. They made a significant contribution to the smooth running of the construction project.’ Their thanks also go to all internal employees who contributed to the planning and implementation of the logistics centre. Höggerl and Neumann also express their gratitude to those responsible at the Müller-Guttenbrunn Group:
‘It was great how we were able to create something new here together.’
Looking to the future: We want to hand over a functioning company to those who come after us
With the construction of the logistics centre, MGG Polymers has reached the end of its construction possibilities at the site – due to the geographical conditions. Roughly speaking, what has now been created must be sufficient for the realisation of other concepts already planned. New technologies are already being worked on in order to get even more out of the available material and to recycle it. The aim must be to increase the depth of recycling and send even fewer fractions to incineration. A pioneering spirit is still required from the recyclers from the Mostviertel region, because the challenges are not getting any less. That’s why MGG Polymers lives true to the motto ‘It’s about CO2’!
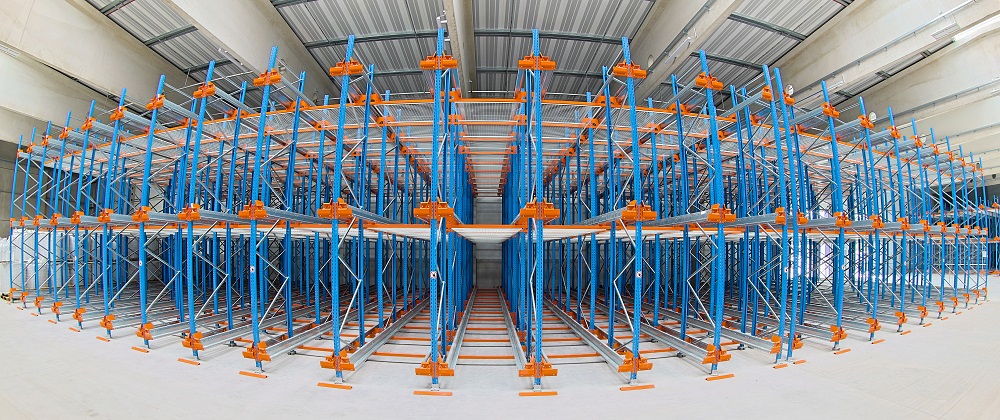
A remote-controlled shuttle system transports the goods to their destination.
Dates, facts & figures
- Start of planning: October 2021
- Start of construction: October 2023
- Completion (planned): End of August 2024
- Total investment amount ‘Growth Strategy 2030’: > 6 million euros
- Usable area of warehouse and office building: 3000 m²
- Built-up area warehouse: 2700 m²
- Warehouse: Multishuttle rack storage with approx. 2400 storage spaces on 3 floors
- 4 loading silos with a filling volume of 55 m³ each