In view of the current energy price development, photovoltaic systems are becoming more and more attractive and lucrative for private individuals as well as for companies. Generating one’s own electricity and thus using sustainable energy is an imperative of our time, and not only for financial reasons. But what to do when the product life of photovoltaic systems has come to an end? What are the challenges involved in recycling PV modules? And: Which processes make economic and environmental sense?
Filling up the sun for 100 years
The 19-year-old Alexandre Edmond Becquerel discovered the photoelectric effect by chance, which was physically explained by Albert Einstein in 1921. This laid the foundation for photovoltaic technology. This technology was used for the first time – after long research – in 1958, when a satellite equipped with solar cells was sent into space. In the 80s, photovoltaics came back to earth and was further developed for private power generation.
In the course of time, the prices for photovoltaic systems became more and more affordable, among other things due to corresponding subsidies from the public sector. In Lower Austria alone, more than 600 MWp (mega watt peak) can currently be achieved. This value must increase to 3000 MWp by 2030 due to climate protection goals of #mission2030. The goal of the Austrian federal government is to obtain 100% of the national electricity consumption from renewable energies.
So far so good. However, photovoltaic systems also have an „expiration date“. As is so often the case, the developers of a new technology have given little thought to the recycling of defective or no longer efficient PV modules. But PV systems also have a limited product life. The logical consequence is growing mountains of PV scrap in European waste collection centers. This is a problem that the Müller-Guttenbrunn Group has taken on and developed a number of recycling ideas for in recent years. So when it comes to discarded PV panels, MGG is once again a technology pioneer in Austria.
How can PV systems break down?
A photovoltaic system is basically built to be robust, as it has to withstand temperature fluctuations from -20°C to +90°C. Only a few events can destroy the modules, such as large hailstones damaging the glass. However, the main reason why PV panels end up in the trash is mostly due to efficiency issues, as old panels that are still in good working order are increasingly being replaced by new and more powerful panels. In addition, the performance of a PV module is only about 80% after 20 years. Therefore, more powerful systems – currently at around 320 watts peak – make more sense for consumers.
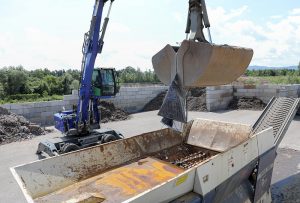
The Miura shredder shreds the photovoltaic elements.
The first challenge in disposing of PV systems is to dismantle them. Even defective panels can, in many cases, continue to produce voltage and emit electricity – if the wires still work. While the majority of panels have a non-conductive aluminum frame, caution is still required. To transport the panels safely, they must be darkened and wrapped. Furthermore, they are placed in additional cover troughs so that they are no longer exposed to solar radiation until the direct recycling process.
The PV panels are shredded at MGG Metran. The scrap is transported to the Miura shredder by wheel loader. In two interlocking rollers, the panels rattle through the shredder and are torn apart into palm-sized pieces. Once the PV system has been torn apart by the shredder, no more electricity flows and thus there is no danger in processing the material further.
A thoroughly complex process up to this point. Metran Managing Director Gunther Panowitz is therefore already thinking about new alternatives: „We are considering recycling directly on site at the collection points. This would save us the long darkening phases. For this to be profitable, however, we need even larger quantities of PV waste.“
Two technologies – one middle ground
Basically, a PV module consists of about 60 % glass with silicon, 10 % aluminum and 30 % other parts such as carrier materials or soft plastic that compensates for the expansion of temperature fluctuations. The plastic particles – also known as „non-target plastics“ – can only be thermally recycled.
For Metran, however, the focus at the end of the day is also on corresponding economic efficiency. Photovoltaic panels have a large volume but little mass. That’s why Metran’s separators first recover all the large pieces of metal, such as aluminum.
Besides aluminum, the really interesting elements that can be scooped out of the glass include copper, tin, lead and silver, which are embedded in the glass in the form of small wires.

After shredding, the PV parts are about the size of a hand and no longer carry electricity.
Currently, Müller-Guttenbrunn uses two different technologies to extract these valuable substances from the shredded material:
On the one hand, the hand-sized glass pieces are further crushed into glass crumbs, from which foam glass, glass beads or flat glass can be produced. In this method, the focus is not on the wires integrated in the glass and thus silicon and metal residues remain in the transparent solid. This shredded glass is not 100% pure and therefore the stability suffers and no first class glass can be recovered in further processing. However, it is sufficient for the production of low-grade glass products.
In order to increase the recycling depth, the PV glass is further crushed and ground into powder form using a hammer mill. Subsequently, the raw materials can be screened out. The focus here is on extracting the precious and semi-precious metals such as copper and silver, as well as the other wires – mainly lead and tin. In principle, the glass can still be melted, but there are few buyers on the secondary market for this end product.
„We started testing these two technologies a little over a year ago with small quantities. In doing so, we asked ourselves which method would suit us best and which end product we wanted to focus on. Although the batches of recyclable photovoltaic modules supplied are steadily increasing, the PV issue is only a marginal topic for us due to the small quantities – currently around 20 tons per month. However, we expect that in the future there will be an increase in the number of discarded modules. Then we will also be prepared to invest further and recycle this special waste fraction,“ reports Panowitz.
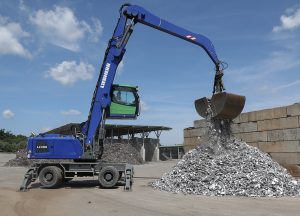
The shredded fractions are collected until larger quantities of PV scrap are gathered for economically viable further processing.
Pioneers don’t have it easy!
Throughout Austria, the Müller-Guttenbrunn Group has once again taken on a pioneering role in the PV module recycling process. „On the one hand, this is good because we are making a name for ourselves with this, but we are only making slow progress in developing the technologies. Also, there is little exchange with photovoltaic manufacturers as they are mainly from China and we face a language barrier. In Germany, photovoltaic systems are already being recycled, but also only on a small scale and, what’s more, with a chemical-solvent-based approach. But here we need other technologies,“ says Panowitz.
Innovation manager Daniel Forstner adds happily: „We are currently in the process of certifying our recycling process. As soon as we receive the Cenelec certificate [note: a certification from the European Committee for Electronic Standardization], we will be able to prove our technological standard to our customers in black and white. This step makes marketing easier for us and the customer knows that we can guarantee him the quality he wants and that we will meet his requirements. In addition to the application areas of large and small electrical appliances and flat panel displays, this would be our fourth Cenelec certificate.“
The bottom line is that Müller-Guttenbrunn is ready for the expected increase in photovoltaic scrap. Assuming an average product life of 20 years, more and more modules will crash through the Miura shredder in the coming years. Above all, however, it would be important for PV producers to incorporate the topic of recycling more intensively into their product development. Because at the end of the day, that’s the only way a proper and sustainable circular economy can work.