In terms of a sustainable circular economy, it has always been a major goal of the Müller-Guttenbrunn Group that manufacturing companies think about the recycling process as early as the manufacturing stage of their products. After all, if used equipment can be recycled easily, the recycling depth increases and the recovery of pure materials from the recycling process is simplified and thus more efficient.
In Fronius, the Müller-Guttenbrunn Group has a cooperation partner for whom the topic of sustainable recycling management is just as important as a producer. For three years now, the research departments of the two companies have therefore been working closely together and exchanging information on an ongoing basis. Fronius is known as a premium manufacturer of inverters for photovoltaic systems. These are used to convert direct current into alternating current. The internationally active manufacturer is known not least for the high quality of its products.
In order to guarantee the desired quality on the one hand, but also to produce as sustainably as possible, the employees of the Fronius research and development department give a great deal of thought to the materials from which, for example, an inverter should be composed so that it is as easy as possible to recycle in the end.
The main components of an inverter include aluminium, engineering plastics, coils, galvanised steel and circuit boards. Since this inverter has to withstand all kinds of weather, great importance is attached to protecting the components. As a result, a minimum service life of 20 years can be expected.
Technical discussions with Fronius R&D staff
To get a feel for how inverters are best recycled, an eight-strong team from Fronius, the manufacturer, was invited to visit the recycling facilities. The team included developers, sustainability management and an external consultant who supports Fronius in the field of life cycle analysis.
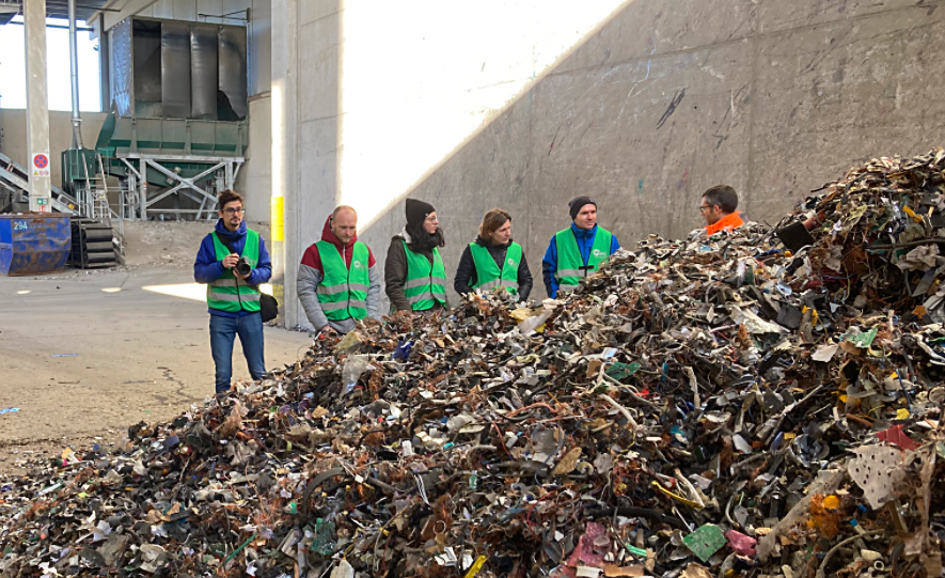
The Fronius team learned more about the individual steps and fractions of the recycling processes during a guided tour.
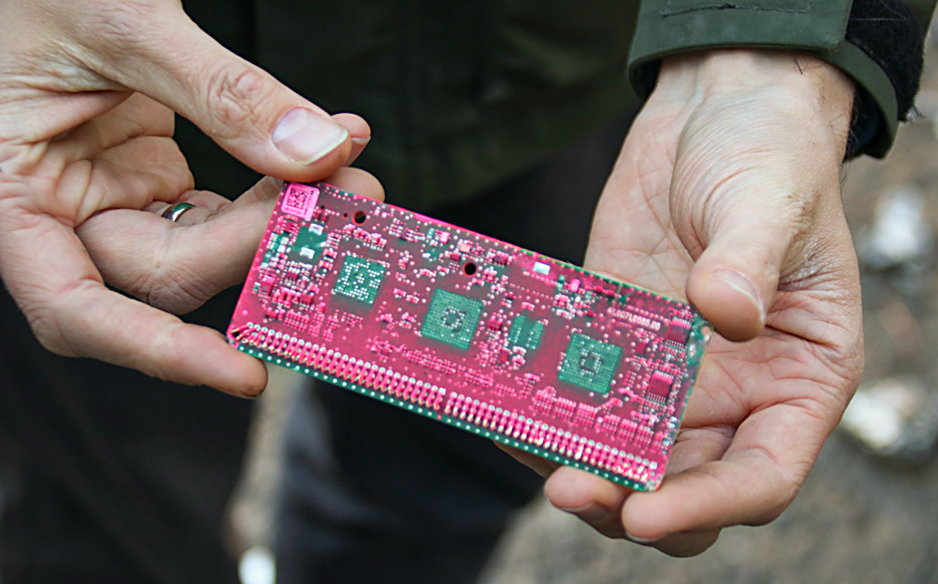
The components of the inverter were sprayed pink before being shredded.
First, a few components of an inverter were shredded at MGG Metrec – in the EVA shredder. These were sprayed pink in advance so that they could then be recognised in the material pile. The inverter parts represent a small amount of material for the large and massive shredder. The bright colour, however, made it easy to find the parts.
Innovation manager Daniel Forstner reports on the initial findings: „The circuit boards themselves are easy to recycle. The challenge is that the potting comes off the board easily and quickly. In addition, you gain valuable copper coils in the course of this process. Recycling the cables built into the inverters also works perfectly.“
Durability or 100 % recyclable?
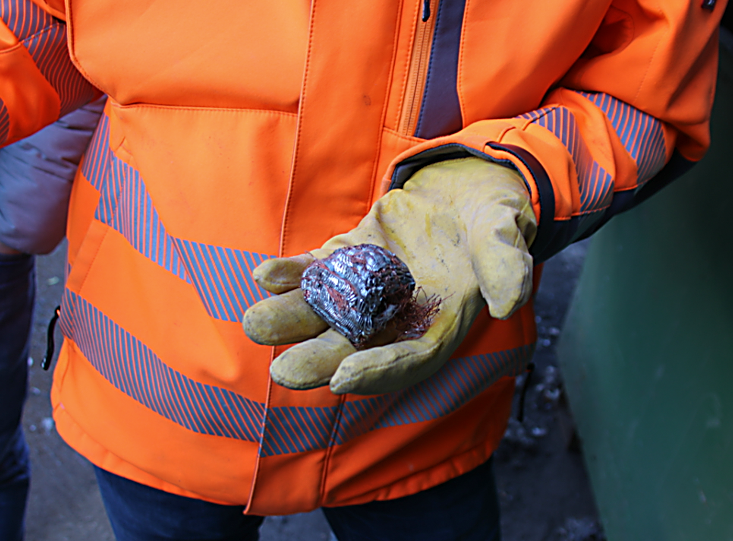
After mechanical treatment in the EVA shredder, inverter coils were sorted out.
The only thing that failed in the shredding attempts was the coating of the inverters. The potting compound has resin components and is therefore not a classic plastic such as ABS (acrylonitrile butadiene styrene) or PS (polystyrene). The only recycling method for the synthetic product is therefore the incineration fraction.
This potting compound is used to protect the metallic and electronic components from wind and weather. It would be possible to do without this coating, but the quality of the product and its longevity would suffer. Daniel Forstner therefore recommended to the Fronius team from an economic point of view: „In the end, it is better to invest in a long product life. It is better to work on making the individual components even more durable in order to increase the life expectancy of the inverters by a few more years. If one were to focus on recyclability, a single, non-sealed inverter would be cheaper to produce and for the consumer, but the customer would need two of these devices compared to a product with potting compound. This means that twice as much material would be needed, and that is not efficient. Besides, Fronius is not a low-cost supplier, but the premium manufacturer par excellence. And at the end of the day, both moulded and non-moulded scrap parts of the inverters end up in the EVA shredder anyway. If you go for high quality, the waste masses remain manageable.“ Fronius is very positive about this recommendation.
Results of the life cycle analysis
Through one of Fronius‘ guiding principles – „Design for Recycling“ – the company has set as one of its top goals to reduce the ecological footprint of its products. The current status of this endeavour and corresponding progress can be determined by life cycle analysis (LCA). In collaboration with external LCA partner Harald Pilz of to4to (together for tomorrow), Fronius conducted a life cycle analysis for the GEN24 Plus inverter in 2020, and this spring completed the LCA for the Tauro Eco 100 commercial inverter. Using the „cradle-to-grave approach“, this inverter was closely examined on the basis of the ISO 14040/44 standards. The following life cycle phases, linked by transport, were considered in the LCA.
- the procurement of raw materials,
- the production phase at the Fronius locations,
- the use phase and
- the end-of-life phase (EOL).
After evaluating all the important data, Fronius comes up with some very pleasing results. Looking at the payback period – the time it takes to offset all CO2 emissions caused by production and transport – the Tauro ECO 100 inverter performs very well. From this point on, the inverter produces „extra energy“ which, depending on the scenario, is up to 62 times higher than the energy required for the entire life cycle of the device.
In total, the transport of materials and components to Fronius, production and transport to the customer account for only a few percent of the environmental impact of the inverters in the entire product life cycle. On the one hand, this is due to the fact that Fronius relies primarily on rail, sea and truck freight, and on the other hand covers 100% of its own energy requirements from green electricity. And when it comes to waste management, the Müller-Guttenbrunn Group is the right partner for the end-of-life devices.
Fronius and MGG comply with all the relevant WEEE directives, and the recycling process means that raw materials and energy sources can be substituted, reducing the inverter’s carbon footprint. So Fronius is on the right track, and through intensive research and the best cooperation partners it will certainly become even more efficient in terms of environmental protection in the future.
Further information regarding the two LCAs, is available for download via whitepaper at www.fronius.com.